About Huntsman
Huntsman Corporation operates as a global manufacturer of diversified organic chemical products. The company operates all of its businesses through Huntsman International LLC (Huntsman International), the company’s wholly-owned subsidiary. The company’s products comprise many different chemicals and chemical formulations, which the company markets globally to a wide range of consumers that primarily consist of industrial and building product manufacturers. The company’s products are used in a broad range of applications, including those in the adhesives, aerospace, automotive, coatings and construction, construction products, durable and non-durable consumer products, electronics, insulation, packaging, power generation and refining. Many of the company’s products offer effects, such as premium insulation in homes and buildings and the light weighting of airplanes and automobiles that help conserve energy. The company is a leading global producer in many of its key product lines, including MDI, amines, maleic anhydride and epoxy-based polymer formulations. On February 28, 2023, the company completed the sale of its textile chemicals and dyes business (‘Textile Effects Business’) to Archroma, a portfolio company of SK Capital Partners (‘Archroma’). Segments The company operates in three segments: Polyurethanes, Performance Products, and Advanced Materials. Polyurethanes The company is a leading global manufacturer and marketer of a broad range of polyurethane chemicals, including MDI products, polyols and TPU (each discussed in more detail below under ‘Products and Markets’). Polyurethane chemicals are used to produce rigid and flexible foams, as well as coatings, adhesives, sealants and elastomers. The company focuses on the higher-margin, higher-growth markets for differentiated MDI-based polyurethane systems and polyurethane component molecules. Volume growth in the company’s Polyurethanes segment has been driven primarily by global economic activity and the continued substitution of MDI-based products for other materials across a broad range of applications. The company operates three major polyurethane manufacturing facilities in the United States (‘U.S.’), Europe and China. The company also operates 26 strategically located downstream facilities, of which 17 are polyurethane formulation facilities, commonly referred to in the chemical industry as ‘systems houses’. The company’s systems houses are located in close proximity to its customers worldwide, which enables the company to focus on customer support, technical service and a differentiated product offering. The company also operates two specialty polyester polyol manufacturing facilities focused on the insulation market, three downstream TPU manufacturing facilities in the U.S., Europe and China and two spray polyurethane foam (‘SPF’) manufacturing sites located in the U.S. and Canada. The company’s customers produce polyurethane-based products through the combination of an isocyanate, such as MDI, with polyols, which are derived largely from PO. The company is able to produce over 2,500 distinct MDI-based polyurethane products by modifying the MDI molecule through varying the proportion and type of polyol used and by introducing other chemical additives to the company’s MDI formulations. As a result, polyurethane products, especially those derived from MDI, are continuing to replace traditional products in a wide range of end-use markets, including insulation in construction and cold chain, cushioning for automotive and furniture, coatings, adhesives, wood binders for construction and furniture, footwear and other specialized engineering applications. The company operates a world-scale integrated polyurethane formulations facility and a world-scale research and development campus in China to service its customers in the critical Chinese market, the largest MDI market in the world, and the company will support the long-term demand growth that this region will continue to experience. Additionally, the company entered into an agreement with Sinopec to form a joint venture to build and operate a world-scale PO/MTBE plant in Nanjing, China utilizing proprietary PO/MTBE manufacturing technology. PO is used in the manufacturing of polyurethane systems and MTBE is an oxygenate used in gasoline. The company owns a 49% interest in the joint venture and account for its interest in the joint venture as an equity method investment. Huntsman Building Solutions (‘HBS’) is a leading North American manufacturer and distributor of SPF insulation systems for residential and commercial applications. The company’s SPF products offer significant environmental benefits, as the company’s proprietary manufacturing process transforms raw material from low quality PET plastic bottles into highly effective energy-saving polyurethane insulation. HBS offers attractive growth potential as energy efficiency standards and requirements increase globally and continue to shift towards a greener economy. Products and Markets MDI is used primarily in rigid foam applications and in a wide variety of customized, higher-value flexible foam as well as coatings, adhesives, sealants and elastomers. Polyols, including polyether and polyester polyols, are used in conjunction with MDI in rigid foam, flexible foam and other non-foam applications. The following chart illustrates the range of product types and end uses for polyurethane chemicals. The company produces MDI, polyols and TPU products and do not produce TDI products. Polyurethane chemicals are sold to customers who combine the chemicals to produce polyurethane-based products. Customers will use either polyurethane component molecules produced for mass sales or polyurethane systems tailored to specific requirements. By varying the blend, additives and specifications of the polyurethane chemicals, manufacturers are able to develop and produce a breadth and variety of polyurethane-based products. MDI MDI is an aromatic diisocyanate molecule used in the manufacture of polyurethane-based products. MDI can be used to make polyurethanes with a broad range of properties and can therefore be used in a wide range of applications. MDI and formulated MDI systems, which combine MDI and polyols, will continue to grow at a multiple of global GDP driven by the megatrends of energy management, food preservation, demographics and urbanization/transportation. MDI offers key products benefits of energy efficiency, comfort and durability aligned with these megatrends. MDI and formulated MDI systems will continue to substitute for alternative materials, such as fiberglass in insulation, phenol formaldehyde in wood binders and TDI in automotive and furniture. Specialty cushioning and insulation applications, thermoplastic polyurethanes and adhesives and coatings will further contribute to the continued growth of MDI. MDI experiences some seasonality in its sales reflecting its exposure to seasonal construction-related end markets, such as insulation and composite wood products. Sales generally peak during the spring and summer months in the northern hemisphere, resulting in greater sales volumes during the second and third quarters of the year. Polyols Polyols are combined with MDI and other isocyanates to create a broad spectrum of formulated polyurethane systems. Demand for specialty polyols has been growing at approximately the same rate at which MDI consumption has grown. TPU TPU is a high-quality, fully formulated thermal plastic derived from the reaction of MDI or an aliphatic isocyanate with polyols to produce unique qualities, such as durability, flexibility, strength, abrasion-resistance, shock absorbency and chemical resistance. The company can tailor the performance characteristics of TPU to help meet the specific requirements of the company’s customers. TPU is used in injection molding and small components for the automotive and footwear industries. It is also extruded into films for apparel, wires and cables for industrial use and in a wide variety of applications in the coatings, adhesives, sealants and elastomers markets. Other Other sales primarily consist of aniline, benzene, nitrobenzene and other co-products, which all are used primarily to manufacture MDI. The majority of the company’s aniline is consumed internally with some sold to third parties. The lack of a significant spot market for aniline means that in order to remain competitive, MDI manufacturers must either be integrated with an aniline manufacturing facility or have long-term, cost-competitive aniline supply contracts. The company’s strategy is focused on growing its differentiated product offering (differentiated MDI and polyols, formulated MDI-based systems and TPU), which requires a greater emphasis on formulating capability and technical solutions to help the company’s downstream customers meet the desired effect required in their applications. Sales and Marketing The company markets its polyurethane chemicals to over 6,300 customers in more than 90 countries. The company’s sales, marketing and technical resources are organized to support major regional markets and key end-use markets, some of which require a coordinated global approach, such as key accounts across the automotive and elastomers markets. These regional key end-use markets include the company’s insulation businesses, footwear, furniture and other construction and industrial markets. The company sells both directly and indirectly to customers, the latter via a network of distributors and agents who in turn sell the company’s products to customers who cannot be served as cost effectively by the company’s internal sales groups. The company provides a wide variety of polyurethane solutions as components (i.e., the isocyanate or the polyol) or in the form of ‘systems’, in which the company provides the total isocyanate and polyol formulation to its customers. The company’s ability to deliver a range of polyurethane solutions and technical support, which can be tailored for the needs of the company’s customers, is critical to the company’s long-term success. The company has strategically located its downstream polyurethane systems houses close to the company’s customers, enabling the company to focus on customer support and technical service. This customer support and technical service system contributes to customer retention and also provides opportunities for identifying further product and service needs of customers. The company’s strategy is to grow the capabilities of its downstream facilities both organically and inorganically. As a result, the company has made a number of ‘bolt-on’ acquisitions in the last decade to expand the company’s downstream footprint and align with the company’s strategic intent. Along with this, the company continuously evaluates its global footprint to better utilize the company’s assets and systems houses while providing strong customer support and technical service. Manufacturing and Operations The company’s world-scale MDI production facilities are located in Geismar, Louisiana; Rotterdam, the Netherlands; and Caojing, China. These facilities receive aniline, which is a primary material used in the production of MDI, from the company’s facilities and third-party suppliers. At the company’s Geismar, Rotterdam and Caojing facilities, the company utilizes sophisticated proprietary technology to produce MDI. This technology contributes to the company’s position as a MDI producer. The company’s global production capacity of MDI, polyols and TPU is approximately 2.8 billion pounds, 0.7 billion pounds and 0.1 billion pounds, respectively. Key Joint Ventures Rubicon Joint Venture: Lanxess AG (‘Lanxess’) is the company’s joint venture partner in Rubicon LLC (‘Rubicon’), which owns aniline, nitrobenzene and DPA manufacturing facilities in Geismar, Louisiana. The company is entitled to approximately 78% of the nitrobenzene and aniline production capacity of Rubicon, and Lanxess is entitled to 100% of the DPA production. In addition to operating the joint venture’s aniline, nitrobenzene and DPA facilities, Rubicon operates the company’s wholly-owned MDI, polyol and maleic anhydride facilities at Geismar and is responsible for providing other auxiliary services to the entire Geismar complex. Chinese MDI Joint Venture: On January 31, 2024, the company completed the planned separation and acquisition of assets of Shanghai Liengheng Isocyanate Investment BV (‘SLIC’), the company’s manufacturing joint venture with BASF and three Chinese chemical companies. Following the separation, the company operates an independent manufacturing facility at its site in Caojing, China producing crude MDI. This facility is part of the company’s existing Huntsman Polyurethanes Shanghai Ltd. (‘HPS’), site, which is the company’s splitting joint venture with Shanghai Chlor-Alkali Chemical Company, Ltd that also manufactures pure MDI, polymeric MDI, MDI variants and formulated MDI systems. The company owns 70% of HPS. Chinese PO/MTBE Joint Venture: In November 2012, the company entered into an agreement to form a joint venture with Sinopec. The joint venture involved the construction and operation of a PO/MTBE facility in China. Under the joint venture agreement, the company holds a 49% interest in the joint venture and Sinopec holds a 51% interest. Competition The company’s major competitors in the polyurethane chemicals market include BASF, Covestro, Dow, Lubrizol and Wanhua Chemical Group. The company’s competitors in downstream markets include Carlisle Construction Materials, Coim and Lubrizol. Performance Products segment The company’s Performance Products segment has leading global positions in the manufacture and sale of amines and maleic anhydride and serves a wide variety of consumer and industrial end markets. The company’s Performance Products segment is organized by region and product family: amines (both performance amines and ethyleneamines), as well as maleic anhydride. The company produces a wide range of amines in seven manufacturing facilities in North America, Europe, the Middle East and Asia. The company is the largest global producer of polyetheramines, the largest producer of 2-(2-amino ethoxy) ethanol (sold under the company’s DGA brand), the largest global producer of the full range of ethyleneamines and a leading global producer of low emission polyurethane catalysts. The company is the only producer and largest supplier of propylene carbonate and ethylene carbonate in North America. The company is the largest producer of maleic anhydride outside of China and the second largest globally with three production facilities in North America and Europe. Products and Markets Amines Amines are a family of intermediate chemicals that are produced by reacting ammonia, or an alkylamine, with various ethylene and propylene derivatives. The company’s ethyleneamines are manufactured by reacting EDC and caustic soda with ammonia to produce a range of various ethyleneamines homologues having different molecular weights. Most other producers utilize a reductive amination process, which yields a light slate of ethyleneamines. The company’s heavier slate of homologues allows access to a greater range of markets. The company’s amines are used in a wide variety of mainly industrial applications, including composites, paints and coatings, fuel and lubricant additives, agrochemicals, gas treating, oilfield chemicals, polyurethane insulation and flexible foams, semiconductor manufacturing and solvents. The company’s amines customers include Afton, Bayer, Chevron Oronite, DuPont, Evonik, Infineum, Lubrizol, Olin, PPG and Quadra Chemicals. Maleic Anhydride Maleic anhydride is a highly versatile chemical intermediate used for products sold into construction, infrastructure, industrial and marine applications. Notably, maleic anhydride is used to produce unsaturated polyester resins (UPRs), which are mainly used in the production of fiberglass reinforced resins. Maleic anhydride is also used in the production of lubricant additives, as well as food additives and artificial sweeteners. Maleic anhydride is produced by oxidizing either benzene or normal butane using a catalyst. The company’s maleic anhydride technology is a proprietary fixed bed butane-based process with a solvent recovery and refining system. The company’s process is superior in the areas of feedstock and energy efficiency and solvent recovery. The maleic anhydride-based route to BDO manufacture is the preferred process technology and is favored over the other routes, which utilize PO, butadiene or acetylene as feedstocks. As a result, the growth in demand for BDO supports growing demand for the company’s maleic anhydride technology. The company’s maleic anhydride customers include Afton, BASF, Chevron Oronite, Infineum, Ingevity, Primient and Solenis. Sales and Marketing The company sells approximately 250 products to over 850 customers globally through the company’s regional sales and marketing organizations, which have extensive market knowledge, considerable chemical industry experience and well-established customer relationships. In more specialty products for certain markets (e.g., coatings, fuel additives, epoxy-based composites, construction, automotive, polymer modification, energy and semiconductor manufacturing), the company’s marketing efforts are focused on how its product offerings perform in customer applications. The company provides extensive pre- and post-sales technical service support to its customers. The company’s research and development function creates solutions to meet its customers unique and changing requirements. These technical professionals interact closely with the company’s marketing managers and business leadership teams to help guide future offerings and market approach strategies. In addition to the company’s focused direct sales efforts, the company maintains an extensive global network of distributors and agents that also sell the company’s products. These distributors and agents typically promote the company’s products to smaller end-use customers who cannot be served as cost effectively by the company’s direct sales forces. Manufacturing and Operations The company’s Performance Products segment has the capacity to produce a variety of products at 10 manufacturing locations in North America, EAME and APAC. The company’s global production capacity of amines is approximately 0.9 billion pounds and the company’s North America and EAME production capacity of maleic anhydride is approximately 0.6 billion pounds. The company’s amines facilities are located globally. Several of the company’s facilities are located within large integrated petrochemical manufacturing complexes. These include the company’s maleic anhydride facilities in Pensacola, Florida, Geismar, Louisiana and Moers, Germany; the company’s amines facilities in Freeport, Texas and Port Neches, Texas; and the amines facility of Arabian Amines Company (‘AAC’), the company’s consolidated manufacturing joint venture with the Zamil Group in Jubail, Saudi Arabia. Joint Venture The company consolidate the results of AAC, the company’s 50%-owned manufacturing joint venture with the Zamil Group. AAC operates an ethyleneamines manufacturing plant in Jubail, Saudi Arabia. The plant has an approximate annual capacity of 70 million pounds. The company purchases and then markets all the production from this joint venture. Competition The company’s global competitors include BASF, Delamine, Dow, Evonik, Nouryon and Tosoh. The company’s competitors include AOC, Bartek, INEOS, Lanxess and Polynt-Reichhold. In the company’s maleic anhydride technology licensing market, the company’s primary competitor is Conser. Advanced Materials segment The company’s Advanced Materials segment is a leading global manufacturer and marketer of technologically-advanced epoxy, phenoxy, acrylic, polyurethane, mercaptan and acrylonitrile butadiene-based polymer products as well as carbon nanomaterials. The company focuses on chemical compounds and formulations that are used to address customer-specific needs in a wide variety of industrial and consumer applications. The company’s products are used either as replacements for traditional materials or in applications where traditional materials do not meet demanding engineering specifications. For example, structural adhesives are used to replace metal rivets and advanced composites are used to replace traditional aluminum panels and other steel materials to lighten structures in aerospace, automotive and other transportation. The company’s Advanced Materials segment is characterized by the breadth of the company’s product offering, its expertise in complex chemistry, the company’s long-standing relationships with its customers, the company’s ability to develop and adapt its technology and the company’s applications expertise for new markets and new applications. The company operates synthesis, formulating and production facilities in North America, Europe, Asia and South America. The company sells to over 1,700 customers in the following end markets: aerospace, automotive, oil and gas, liquid natural gas transport, coatings and construction, printed circuit boards, consumer, industrial and automotive electronics, consumer and industrial appliances, electrical power transmission and distribution, recreational sports equipment, medical appliances and food and beverage packaging. Products and Markets Aerospace The company’s Advanced Materials segment is a leading global supplier of advanced, high-performance materials for the fabrication and repair of aircraft components. The company supplies leading aerospace companies with innovations in composites, adhesives, laminating and repair systems, alongside innovative carbon nanotube technologies. The company offers a wide range of materials to the aerospace market under the ARALDITE, EPIBOND, EPOCAST, URALANE and MIRALON brands. Many of these products are qualified under the specification of major aerospace original equipment manufacturers (‘OEMs’), complying with appropriate regulations governing large civil aircraft. Automotive The company offers to the automotive market, including leading automotive OEMs and Tier 1 suppliers, high-end composite and adhesive formulations, specialty resins and toughening agents. Lightweight, strength, flexibility, shorter cycle time and fatigue resistance are key requirements of the company’s industrial partners. The company’s Advanced Materials segment has a long history of delivering a wide range of solutions meeting stringent requirements for automotive electronics applications, such as high temperature and chemical resistance, flame-retardancy and excellent mechanical and dielectric properties. The strong global push for electric vehicles opens new opportunities in electric motor thermal management, hydrogen storage systems and battery performance enhancement with the company’s innovative encapsulants, composite systems, toughening agents and carbon nanomaterials. Electrical Infrastructure The company is a leading global supplier of insulating materials for motors, generators, switchgears, distribution and instrument transformers, and insulators and bushings for electrical power applications. The products formulated by the company’s Advanced Materials segment are designed to provide the electrical equipment an extended service life and meet specific industry requirements for electrical insulation in indoor and outdoor environments. Coatings Infrastructure The company offers expertise in curing and toughening technologies and a portfolio of specialized resins and additives to the manufacturers of paints and construction materials. The company’s product technologies, including epoxy hardeners, phenoxy and acrylonitrile-butadiene reactive liquid polymers and high solid or water-based components, enable customers to address challenging industry requirements, such as resistance to aggressive chemicals and high temperature, adhesion to difficult substrates, excellent mechanical properties, high drying speed and easy re-coatability, low temperature and sub-zero cure and low VOC and environmental impact. General Industry The company offers high-performance adhesives and composite formulations, specialty resins, toughening agents and rubber polymers to a large variety of industrial applications, such as sport equipment, leisure and shipping boats, engineering machineries, consumer electronics, rubber consumables and the do-it-yourself market. ARALDITE is an important brand in high-performance adhesive technologies. The company offers formulation expertise in various chemistries, including epoxies, polyurethanes, methacrylates, phenolics, mercaptan and acrylonitrile-butadiene-based polymer products. The company’s materials address requirements such as long open times for large area applications, fast-curing adhesives for early removal and rapid through-put, resistance to high temperature, water and chemicals, thixotropy for gap-filling or vertical applications, and toughness, impact-resistance and elasticity to cope with different thermal expansions when bonding larger structures. The company’s adhesives are used in a large variety of industrial applications. Sales and Marketing The company maintains multiple routes to market to service its diverse and fragmented customer base throughout the world. These routes to market range from using the company’s own direct sales force, distribution to mass distribution. The company’s direct sales force focuses on engineering solutions for its major customers who purchase significant amount of product. The company uses specialist distributors to augment its sales effort in niche markets and applications. The company uses mass general distribution channels to sell its products into a wide range of general applications where technical expertise is less important. The company’s use of multiple routes to market enables the company to reach a broader customer base. The company conducts sales activities through dedicated regional sales teams in EMEAI, Asia and the Americas. The company’s global customers are covered by key account managers who are familiar with the specific requirements of these customers. The management of long-standing customer relationships is critical to the sales and marketing process. Manufacturing and Operations The company is a global business serving customers in three principal geographic regions: EAMEI, Asia and the Americas. In order to service the company’s customers efficiently, the company maintains both synthesis and formulations manufacturing plants around the world with a strategy of global, regional and local manufacturing employed to optimize the level of service and minimize the cost to the company’s customers. The company is completing the build and commissioning of a pilot plant in San Antonio, Texas specifically designed to produce high-value MIRALON carbon nanomaterials, as well as clean hydrogen for sale into the hydrogen market. This pilot plant will demonstrate improved production capability and production of carbon at significantly higher volumes than has historically been produced at the company’s Merrimack, New Hampshire research and development site. This reactor design will form the basis of a larger kiloton (carbon) scale commercial reactor, which will address the needs of markets, such as battery additives and provide a commercial scale source of hydrogen for applications in chemical production and other process industries. Competition The company operates dedicated technology centers in Basel, Switzerland; The Woodlands, Texas; Merrimack, New Hampshire, and Shanghai, China in the support of its product and technology development. Aerospace: The company’s major competitors include 3M, Henkel and Sumitomo. Automotive: The company’s major competitors include Kaneka, Taiyo and Westlake. Electrical Infrastructure: The company’s major competitors include Aditya Birla, Nagase, Westlake and Xiongrun. Coatings Infrastructure: The company’s major competitors include Aditya Birla, Allnex, Evonik, Kukdo and Westlake. General Industry: The company’s major competitors include 3M, Henkel, ITW and Parker Hannifin. Intellectual Property Rights The company owns approximately 2,610 unexpired patents and has approximately 970 patent applications (including provisionals) pending. The company has associated brand names with a number of the company’s products, and the company has approximately 2,915 trademark registrations and 132 pending trademark applications globally. These registrations and applications include extensions of protection under the Madrid system for the international registration of marks. Regulatory Matters The company’s domestic operations are subject to the U.S. Environmental Protection Agency’s (the ‘EPA’) GHG regulations. Some of the company’s facilities are also subject to the EPA’s Mandatory Reporting of Greenhouse Gases Rule. The company is already managing and reporting GHG emissions, to varying degrees, as required by law for the company’s sites in locations subject to the U.S. federal and state requirements, Kyoto Protocol obligations, and/or ETS requirements. History Huntsman Corporation, a Delaware corporation, was founded in 1970. The company was incorporated in 1994.
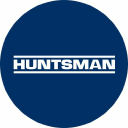